认 证:工商信息已核实
访问量:500957
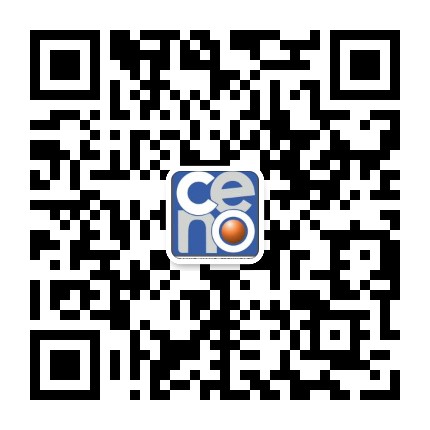
上海矽诺国际贸易有限公司 2020-08-12 点击1010次
分散染料最早被用于醋酸纤维的染色。由于该染料几乎不溶于水而是悬浮、分散于水溶液中上染纤维,所以,1953年后被称为分散染料。自1970年开始,分散染料作为聚酯纤维染色惟一适用染料,成为所有染料中发展得最快的一类[3]。1976年的《染
料索引》第四版上分散染料品种已达829种,产量仅次于当时的直接染料[4]。
2004年,中国分散染料的年产量突破33万吨,不仅占我国染料总产量的55.2%,而且接近世界分散染料年产量的70%,成为世界上分散染料第一生产大国。但是,我国分散染料总产量的85%~90%都是固体剂型(粉状和粒状),全球比例为67%;而液
状剂型(液状和糊状)的分散染料只占总产量的10%~15%[5]。
染料工业的发展与纺织纤维密切相关。2010年,全球合成纤维生产总量为4298万吨,比上一年增长12.4%,其中全球涤纶产量为3641.3万吨,中国涤纶产量为2513.4万吨,占全球产量的69%,相应分散染料产量为34.95万吨,为国内历年最高,居世界
第一[6]。据统计,2012年,全球涤纶的产量已达4140万吨,作为合成纤维生产大国,中国的涤纶产量也稳步增长,相应我国分散染料产量也增长到41.44万吨,占我国染料总产量的49.7%[7]。2014年我国分散染料产量持续增长,达到44.73万吨,其中偶氮类、蒽醌类、杂环类占比分别约为75%、20%、5%。
分散染料的商品化加工
染料的商品化加工是指原染料滤饼经过混合、研磨,并加入一定量的填充剂和助剂进行加工处理,使之成为标准化商品染料的过程。染料商品化加工有助于稳定染料成品的质量、提高染料的应用性能。
对于低水溶性的分散染料,要求其能在水中迅速扩散,并成为稳定的胶体悬浮液,因此在出厂前,必须对染料要进行商品化处理,分散染料最主要的加工是选择适当的助剂将染料充分研磨制成易于在水中高度分散和稳定悬浮的染料商品。研磨前将染
料、分散剂和其它助剂与水混合均匀,再置于研磨机中进行研磨,直到取样并测试细度及扩散性能达到合格,然后喷雾干燥,最终经混配、标准化达到商品规格[9]。商品分散染料必须满足以下三方面的要求:①分散性,即染料能够在水中迅速分散,成为
均匀稳定的胶体悬浮液;②细度,即染料颗粒粒径在1 μm 左右甚至更小;③稳定性,即染料在放置及高温染色时不发生凝聚现象[10]。
分散染料按照商品化加工剂型,可以分为固状和液状。所谓固状染料,就是包括粉、粒、块状等有固定几何形状的染料剂型。在众多的商品染料中,固状染料无论是品种还是使用量,都处在首要位置,主要是因为固状染料具有贮存稳定性好及包装简单、运输方便、生产技术成熟等优点。而粉状染料又是目前产、销量最大的固状剂型,几乎所有的分散染料都可以加工成粉状剂型。染料滤饼与分散剂混合后进行研磨,使染料固体的颗粒粒径减小到1-2 μm,生成稳定的分散体,再经喷雾干燥即可得到商
品化的粉状分散染料。而液状染料则省去了喷雾干燥过程,它是经过特殊的商品化加工方式得到的,最终的商品形式仍是液体状态。
液状分散染料
目前,分散染料占我国染料总产量的50%以上,我国已成为世界上最大的分散染料生产国,其中固体剂型分散染料占据总产量的绝大部分,而液状剂型分散染料的产量却很小。但是,与粉状分散染料相比,液状分散染料具有诸多无法比拟的优点:①
液状分散染料使用较少的分散剂即可达到良好的分散效果,节约成本且提高了染料利用率;②省去喷雾干燥过程,简化了工艺,节省了能源;③便于自动取料,符合印染工业自动化发展趋势;④从源头上消除了粉尘污染等等,这使其作为分散染料的一种商品剂型近年来又逐渐受到重视。
液状分散染料的发展及现状
自20 世纪60 年代开始,国外液状分散染料的生产加工已经涉及一些品种,而且,国外著名的染料生产企业如山德士、巴斯夫、拜耳、三菱等都在大力研发液状分散染料商品,如Foron P 型、Procilene P 型、Intrasil P 型等。虽然液状分散染料优点众多,但是也有明显的不足,如贮存稳定性差,容易沉淀,导致上下分层,使上下层染料浓度不均一;长时间储存,染料颗粒还容易发生二次团聚,使得粒径变大,影响染料性能。液状分散染料的这个致命缺点严重影响了其推广和使用,因此液状分散染料的生产与应用并未得到普及。
目前,国内外有关液状分散染料的研究报道相对较少。Klaus Hofmann 等[11]制备了80%染料颗粒平均粒径小于1 μm 的液状分散染料,在室温和50 ℃分别放置数月,也未出现分层现象,显示了良好的贮存稳定性。很多外国公司[12-15]也有液状分散染料的品种,但是总的品种数还是相对很少,价格也相对较贵,不能满足大多数印染企业的需求。然而,我国染料工业又长期偏重经典合成工艺的开发,而缺乏对染料商品化、剂型开发的重视,投入的精力和研发经费远远低于原染料的开发。这使得我国染料产品在高附加值上的竞争明显落后于国外公司。国内对液状分散染料的研究积极性也不高,相关的研究大多数都没有推广到工业化生产。
液状分散染料的制备方法
超细液状分散染料的制备方法有很多,大致可以分为化学加工方法和物理加工方法。其中化学加工方法包括乳液聚合法、溶剂法等;物理加工方法有高压均质法、超声波制备法、机械研磨法。与化学加工方法需要使用大量有机溶剂不同,物理加工方法以水为介质,工艺操作简单、高效,且技术更加成熟,是目前被广泛使用的加工方式。
1.2.2.1 乳液聚合法
微乳液法是利用表面活性剂使两种不相溶液体形成热力学稳定的、各向同性、外观透明或半透明且粒径在l~l00 nm范围内的分散体系。Choi等[18]采用乳液聚合法制备出了粒径在110~130 nm的分散染料,且染色试验表明,其对超细涤纶有较好的染色
性能。Fu等[19]也采用细乳液聚合法制备了超细包覆分散染料并将其应用于棉织物的热转移印花
溶剂法
中国专利CNl703465A 报道了溶剂法制备超细分散染料的技术,即采用乙醇、丙酮或苯酚对分散染料进行初步溶解,然后加入去离子水,最后将有机溶剂蒸馏取出并回收,结果制备出了粒径小于100 nm 的超细分散染料[20]。但是,在制备过程中使用
了大量的有机溶剂,导致生产成本较高且不环保。
1.2.2.3 高压均质法
高压均质法是利用流体力学原理,依靠均质机产生60~120 Mpa高压将具有一定粘度的液态物料细化及均匀混合的加工过程。若要把不溶性颗粒粉碎成纳米级粒子且均匀分散在液相中,则同时需要加入分散剂防止小颗粒凝聚。如今有很多均质机能够
加工纳米级均质乳液,如加拿大Avestin公司的高压均质机,意大利NIRO SOAVI公司的高压均质机等[21-22]。
在国内,沈卫庆等[23]利用高压均质机将球磨好的液状分散染料在均质压力为1200 bar 下,均质6 次后,得到了颗粒粒径小、分布窄的染料分散体系。赵国生等[24]将分散黑ECO 按比例与复合分散剂混合,球磨后再经高压均质机均质得到了平均粒径为115 nm 的液体分散黑ECO。
1.2.2.4 超声波制备法
超声波在液体中传播时会产生剧烈的空化效应,利用超声波的空化效应所产生的局部高温、高压、爆炸及微射流等,能够较大程度地削弱纳米颗粒间的结合能,从而有效地避免纳米颗粒团聚,使之充分分散,但不应采用过热超声搅拌,因为随着热能和机械能的增加,颗粒碰撞的概率也增加,反而促使纳米颗粒的团聚。一般超声波空化与机械研磨结合来可以达到更好的分散效果。王平等[25]采用了一种超声波空化加机械研磨的方法来制备超细微粉。结果表明,这种方法可以制造出纳米级的颗粒,而且该方法容易实现工业化。
1.2.2.5 机械研磨法
到目前为止,采用化学法制备纳米粉体方法已在学术界有丰硕的研究成果,但其制造成本相对较高,所得到粒径分布亦较宽。所以至今,企业界仍以物理机械研磨方法制备纳米级粉体为主。物理机械方法较易制得粒径分布较窄的纳米粉体,同时生产成本相对较低,参数容易控制,可以实现批量生产,且产品质量已能满足行业需求[26]。机械研磨分散设备有球磨机(振荡式、行星式、立式、卧式)、搅拌磨(立式、卧式)、离心磨、胶体磨、气流磨、高速冲击磨等[27]。机械球磨法的原理是用外部机械的作用,即通过研磨球、研磨罐和颗粒三者之间的频繁碰撞,颗粒在球磨过程中反复地受到剪切力、摩擦力和冲压力的作用,颗粒表面的缺陷密度增加,晶粒逐渐细化。对于分散染料而言,机械湿法研磨的应用最为普及,因为它具有产量大、成本低、工艺简单,且适宜于大规模生产的优点。
采用球磨机对分散染料进行研磨与分散,其研磨效果主要取决于球磨机转速和研磨珠。在设备允许的条件下,转速越快,研磨效率就越高。研磨珠的种类有很多,如氧化锆珠、不锈钢珠、玻璃珠等。它们的大小和密度均会影响研磨效果,一般认为,
研磨珠的相对密度要与浆料的粘度相适应,高粘度的浆料应选择相对密度大的研磨珠,低密度的浆料则选择相对密度小的研磨珠。而且,若研磨珠越小,研磨珠之间的接触点越多,体积效率也就高,研磨效果更佳,但若研磨珠过小,会产生大量的热量,
使温度上升过快,加剧团聚,同时也会给研磨珠与浆料的分离带来困难。由于在球磨时体系摩擦会生热,可以通入冷却水来降低体系温度。此外,研磨珠的填充量也必须适中,过多会导致产生热量太多;过少使得球磨效率变差。